Introduction: Marshall Union Jack Guitar Amplifier Headshell
2022 was Marshall Amplification's 60th anniversary. I needed a new project and to build an iconic design that celebrated the 'Father of Loud' Jim Marshall and his company. Nothing says Made in England like the British Union Jack flag.
Supplies
The shell is made from curly maple for the white sections and curly maple dyed with RIT fabric dye Sapphire Blue for the blue bits. The red is red heart.
Step 1: Plotting the Union Jack
Plotting the Union Jack. There is a method to the ratios and angles used on the Jack. I found the details at Flag Institute here and will summarize the details a bit. The ratios for the stripes are 1 unit for the thin, 2 units for the medium and 3 units for the thick. The angles are 30.96° which I have rounded up to 31° - apologies to all Brits for taking the easy way out. Moving clockwise the angled stripes have the thick white section on the leading edge.
There is a land and a naval version - the top to side ratios are different. Since amplifiers and water don't play nice this one is the land version modified to fit the necessary dimensions of Marshall's small box cab - 24"x10.25"x8.5"
I drew this out in an ancient copy of AutoCAD to keep my design honest. I also planned on the top and front to have gaps for airflow and only had the blue bits move in enough to support the structure. This also gave me the necessary stripe widths and data to build a jig - more on that later.
Step 2: The Wood
I am a huge fan of curly maple for it's amazing figure and ability to take the fabric dyes I prefer to use when looking for colors that POP! For the 'cool' side of the color wheel - blues, greens, purples - the wood may need to be bleached with a two part process of 10% bleach and a strong hydrogen peroxide to neutralize the bleach. Otherwise the color ends up looking like brown was added. Household bleach is 2% so the wood version will cause pain and gloves and eye wear is a smart move.
Fortunately, I found some maple that took the blue dye well. But first it's time to cut!
Step 3: Cutting the Jack Stripes
First I trimmed the maple and red heart planks to 'working' length - typically 1/2" more than is required to allow for trimming to finish length. I used a 10" Rikon bandsaw with a Woodslicer blade that is designed for book matching wood with a minimum of wastage. I typically cut a few more than needed as the dreaded WHOOPS - insert your favorite power word here - making it easy to grab another piece.
One thing about cutting wood - in the beginning I tried to 'save' as much as I could by cutting as short as possible or trying to get as much out of a piece as I could. Inevitably the design was compromised or I had to cut more wood to save the design intent. My first piece of figured wood - cherry, pictured - I so afraid of cutting it 'wrong' that it sat in a friend's shop for 3 months before I dared to cut it.
Step 4: Stripe Gluing
A flat surface, wax paper and clamps, clamps and more clamps. You can't have enough clamps. 24 hours to full cure.
I use Titebond III as it's water resistant which I suspect - hope - will give some protection against humidity AKA water vapor causing unhappiness. The nice thing about modern glues like Titebond the joint is stronger than the surrounding wood. On the cherry cab shown above I glued supports at the wrong angle and didn't discover it until the following day. I thought I could whap them out with a mallet. Nope. Bigger hammer and a block of wood and serious effort. Double nope.
Don't worry I have many more clamp pictures to follow.
Step 5: Main Cross Cut and Glue
In the interest of sanity and preserving what hair remains to me I refuse to cut 45° intersections that the white stripes surrounding the main horizontal and vertical red stripes. I butt jointed the white bits instead. As you can see lots and lots of clamps to make sure that all pieces are held firmly to the table top. Nothing causes power words to erupt when it's discovered that one piece isn't flush. This is one of the reasons I limit the number of pieces for each glue step.
Step 6: Cutting the Angles
I don't like cutting angles, so much can go wrong. Generally when I build a fixture I have to tweak once or twice to get the desired result. The 31° fixture was a first - not only did it work correctly on the horizontal but it could also cut the opposing vertical 59° needed on the mating side. As you can see due to the short stripe lengths it was uncomfortably close to the blade requiring maximum focus and total awareness of where my fingers were. A table is one of the most useful tools in the shop and the most dangerous as it can lop off the odd finger before you notice you've been cut. Guitar and nose pickers really need their fingers.
Step 7: Gluing the Angles
Plowing ahead with more gluing. I like to use lots of force to keep wood from shifting. For this section that was a bit of a train wreck. The more pressure I applied on one end caused the other end to shift. So lots of back and forth - a little here, a little there - did anything shift? No. Then just a bit more.
Then resist the temptation to apply just a 'bit' more. Must walk away.
I dyed the blue bits just to get a sneak peek on the colors together. I ran the finished Jack through a drum sander to mill to my preferred 3/4" thickness which took off the blue.
Step 8: Choosing the Blue
As I mentioned before I'm a bit fan of RIT fabric dyes as they're water based and yields a richer color and they have lots of hues that just POP! No offense to traditional wood stains / dyes but they are generally low impact and boring. I want IMPACT!
I am a firm believer in experimentation to find the best color for the wood being used. This is where that scrap wood comes in handy or if you have a hidden surface use it. My Birdseye maple dining table has twelve 12" squares of varying dyes on the underside in the search for the perfect one.
Of the four darkish blues I have on hand and the Sapphire Blue was the clear winner. The Royal Blue was too purple.
Step 9: Cutting the Sides
The sides will be blue, white with the red heart center stripe - five pieces in all. I chose this method as it will be easier to keep the white section the correct width when it comes time to dye the outer bit blue as there will be a guiding line.
I'll cut the handles later.
Step 10: Finger Joint Time
I use a homemade jig for finger joints and Freud's excellent Super Dado. I've use several including one that was $100+ more but unlike the others when I stack blades for a .750" cut they measure .750". No shimming with shims or paper to get to the desired width. They are carbide and give a great finished cut.
One note - if you're using a dado and one of the blades or clippers cuts a trough lower than the others you have a low spot on your saw's spindle. Make a mark so you can track your position then loosen turn the spindle and retighten the blades and make a test cut. Rinse and repeat until they are all flat. I took a file and made a notch on the blade backer where the spindle is level and problem solved.
I like vise grip or Krieg style clamps to hold the wood steady and if something happens I can let go of the plank and not worry about it flying back at 'flung from a table saw' speeds. This is very exciting and worth avoiding.
The planks are .100" or more larger than finish thickness to remove any tear out from jointing, then I run them through a drum sander until they are at the desired thickness. As shown I cut two thinner pieces the width of the blue stripe for the bottom - no sense in wasting more wood for a side that won't be seen. Narrow pieces require more care to keep them 90° to the blades.
The remaining open finger joint cuts get filled with 'fake' fingers oriented to mimic the wood grain orientation.
Step 11: Handle?!? Oh No!
Unfortunately, the top opening on the Jack doesn't work comfortably for a handle. Adding a traditional style amp handle -pictured - is like putting white wall tires on a Porsche - yuck.
The alternative was cutting chevrons at the same 31° angle as the stripes. I contemplated doing a mock Jack with another reversed chevron below and a couple of horizontal slots, but I have enough foolishness going on with this that I chose not to.
Holes were drilled with a Forstner bit that cuts flat on the bottom for neater holes. Saber saw cuts to connect them and Dremel and files to finished shape. I put a bit of round over for finger comfort.
Step 12: Prep for Roundover
Marshall amplifier cabs have a metric round over - I do a 3/4" with a high angle wood plane and an orbital sander. I draw witness lines at 3/8" & 3/4" on both faces then cut a 45° bevel with the plane then 60-80 grit sandpaper in an orbital sander - one of my favorite tools as it reveals the beauty of the wood figure as I work through 80, 150 & 220 grit disks. After the 45° is cut I sand in bevels around 60° then a swipe at 75° [ish]. Then starting from one face I round over the corner with successive edge crossing passes until its round. It takes a bit of practice to master but it has two huge advantages over a router - ZERO tear out and it's significantly quieter. It is slower.
There are images with the completed round over to be revealed ahead.
Step 13: Enter the Faceplate
One challenge of stripes is lining up bits on another face. I won't bore you with a repeat of gluing up. I tend to be a trimmer - test cut - check, another test cut check. Hopefully to success. With the main vertical stripes lined up the rest fall into place easily. Marshall uses a plastic strip called piping to wrap around the faceplate with a contrasting color - typically gold. I'm going to use a strip of curly maple about 1/8" thick and leave it white.
I use a shooting sled which has clamps to hold the work as the edge gets cut straight. I also used it to cut the bottom section out for the amp control panel.
The piping is attached with recessed screws as it will be attached and taken off a few times before final installation.
Step 14: Logo Time
I toyed with several iterations of a logo combining 60 with Marshall and elected to do my version of the Marshall logo.
I draw it then use a Stewmac plunge router fixture for Dremels and a 1/32" tapered router bit to carve out the logo. It takes about an hour to do. I filled the cutout with a mixture of epoxy tinted with pearl powder. It takes 24 hours for the epoxy to cure then I sand it level with the wood.
Step 15: Dye and Lacquer
Before I apply the blue dye, I brush on a thin bead of lacquer on the white stripes border to form a barrier to keep the dye from drifting. Then with a bit of t-shirt, wipe on a couple of coats of the blue with vigor like it owes you money. I dry it with a hairdryer as I'm impatient.
I have a pair of pine L frames I built for finishing as the frames only touch the inside of the cab / box as it's rotated about to apply the lacquer. I used to use brush lacquer and it works well on flat surfaces which the Jack lacks. I switched over to Minwax gloss spray lacquer as it gives a great finish cures quickly and is very forgiving.
I was spraying a speaker cab one night and it was a bit warm in the shop as I can't run fans during application. I use a vapor level two filter mask that is so good I can't smell the spray. As I finished the top - naturally - a drop of sweat dropped onto the surface I had just sprayed. I stared at it for a second - yes, power words were spewed - then grabbed a piece of paper towel and 'rolled' up the sweat. A couple of shots on that spot and I resprayed that side again. No evidence left - I'm a believer.
I hold the can about 8-10" away [I'm spraying at an angle] and a overlap by 50% the previous pass as I work my way across the side. Then repeat the same side again. Roll to next side and repeat. Wait 20 minutes and go again. In an hour I can put down about 6 coats which is enough to me.
Step 16: Assembly and Other Small Bits
Time to install the amp. I use oxide finished flat head screws to secure the amp as I think a countersunk hole is more attractive than a roundhead with a washer sitting above the surface. I calculate the faceplate thickness and the amount of offset [pushed into the head shell] and use that to position the amp on the bottom of the head shell for screw hole placement.
To combat RF / extraneous signals from turning the amp into a radio I have aluminum tape which sits on the underside of amp chassis. I use 1.5"x.75" rubber feet - alas, no pics - as they give enough clearance for handles on other amplifier / speaker cabs.
I used neodymium magnets to secure the faceplate for easy removal.
All in all this was a challenging and fun project and I've build a semi wavy variation. This particular piece was selected for display in the Eastern Tennessee Master Woodworkers show in Knoxville TN in early November.
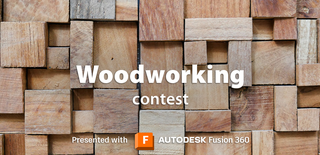
This is an entry in the
Woodworking Contest
Comments