Introduction: Turning a Wooden Pen With Inlays
I recently started on a set of turned pens made from native New Zealand timber and incorporating the colors of the country's fantastic and unique birds using synthetic mica powder (fluorophlogopite). This instructable presents the creation of our fat, flightless and very endangered ground-dwelling parrot, the kākāpō.
Supplies
Woodturning lathe
Pen blank - 2 x 2 x 12 cm
Pen kit (I used a simple slimline pen kit)
Brad drill bit (to fit the pen kit you are using)
Pen mill cutter (to fit the pen kit you are using; you can also use a benchtop sander if you don't have one)
Jacobs chuck (you can use a drill press, but it takes some finesse!)
Synthetic mica powder (while synthetic, fluorophlogopite is not a plastic)
Glue accelerator (optional but useful)
Sandpaper - grits 120 - 1000 (or up to at least 2000 if you are not using micro-mesh pads)
Micro-mesh sanding pads (optional; you can also use wet-sanding paper in 1000 - 2000 grits)
Wax/polish (I used a carnauba car cream/polish)
IMPORTANT SAFETY NOTICE: I am creating this instructable assuming that you know how to use a lathe and lathe tools, and take the precautionary safety measures when doing so. Always wear face and ear protection and a mask - safety first!
Step 1: Cutting the Pen Blank Into Two Barrels
The process, briefly, will go as follows:
- Cutting the pen blank
- Drilling the pen tube holes
- Squaring down the ends of the two pen blanks
- Glueing in the pen tubes
- Mounting the pen barrels on a pen mandrel on the lathe and turning the square blanks into round pen barrels
- Cutting the channels for the mica powder inlays
- Adding the inlays
- Sanding and polishing
- Putting the pen together
Let's go! 👍
Take your pen blank and before (vertically) cutting it into two, draw a directional arrow on one side (horizontally). This will help to ensure that you line up the grain correctly when it comes to mounting the blanks on the lathe and turning them down into barrels.
Using the pen tubes from your pen kit, measure each barrel blank (the front and back barrels of the final pen), giving yourself a bit of leeway on either side of the blank for when glueing in the tubes and trimming down the blanks (see image). You want the wood blanks to extend past the pen tubes (just slightly, maybe .3 cm) once they have been glued into the blanks. This excess will be trimmed so that the pen tubes inside the wood blanks are flush with the edges of the blanks. After measuring both barrels on the uncut pen blank (including the excess on the ends) trim off any excess from the original (2 x 2 x 12 cm) blank. You should now have a pen blank that has two sides of the same length. Cut the blank in half.
Once you have cut the pen blank in half, mark one side on each of the two blanks across (see image) to get the centre.
Step 2: Drilling the Tube Holes
Mount each blank on the lathe in a chuck (one by one), with the centre point showing, and push the blank as far back as possible into the chuck to keep it steady. Mount a Jacobs chuck in the tailstock of the lathe and the corresponding brad point drill bit for your pen's pen tubes in the chuck to drill the hole in the blank for your pen tube (the pen kit should state this, or ask someone where you are buying it for the corresponding bit. I find a nr 7 to be fairly standard for a slimline pen, but do check to make sure). Make sure that the drill point is centred on the blank. Lock down the tailstock and ensure that the wood blank is securely set in the chuck.
NOTE: You can use a normal drill bit in the required size. However, using a brad bit will help to ensure centering the drill bit, courtesy of the point-end that extends at the front of the bit.
Turn the lathe speed down slow and advance the Jacobs chuck using the tailstock turning handle. Do this slowly, and repeatedly draw the drill bit back to remove shavings. The drill bit gets hot quickly and if not pulled back out consistently can throw off the drill bit direction, which will lead to your pen tube not fitting properly. Drill all the way through the blank.
Repeat the process for the second barrel blank.
Step 3: Glue the Pen Tubes and Square Down the Blank Ends
Before glueing the pen tubes into the blanks, take a 100-grit sandpaper and lightly sand down the outside of both tubes; this will help the glue to gain better purchase on the wood and ensure the tubes glue in properly. I use a medium CA glue for this step. Liberally coat the tubes all around and press them into the hole you drilles in the barrel blanks. Leave a small excess area on each side (the excess that was accounted for when you cut each blank) of the blank; this will be used from trimming the blanks flush with the tube.
I typically leave the glue on these to dry for at least 30 minutes to ensure they will not move when milling down the edges (the milling bit can get hot!)
To mill the blanks down, remove the brad drill bit and replace it with a milling bit (the entry point should match the brad bit size for your pen kit). At the same lathe speed as drilling the pen tube holes, slowly advance the tail stock until you have milled down BOTH ends of each blank so that the end of the pen tubes on both sides are flush with the ends of the blank. Don't mill down past the tubes or you may have trouble with the final fit of your pen!
IF YOU DON'T HAVE A MILLING BIT:
A simple solution here is to use a benchtop sander to remove any excess from the ends of the blank. Just make sure that they are sanded flat. Alternatively, you can also trim them down on the lathe once they are mounted on the pen mandrel.
Step 4: Mounting, Trimming and Shaping the Blanks
Remove the chuck from the lathe and mount the pen mandrel. Next, mount the pen blanks on the pen mandrel, using the arrow you marked on the pen blank before cutting it to ensure that the grain lines up. I use a skew chisel to trim down the blanks at a high lathe speed. Since I am going to be adding inlays to the pen, I don't trim the blanks down all the way yet. At this point, I also start shaping the blanks into the general shape I want the final pen to be.
NOTE: If you don't plan on adding inlays, trim the blanks down to their final shape and skip to step six.
Step 5: Adding the Inlays
The absoloute pumpkin that I am, I neglected to take images of the channels I cut into the pen blank before adding the mica powder. However, since this is an aesthetic choice that can be executed in whatever way you like, it doesn't really matter. (Included in the images here is an image of cut inaly channels for a different, darker pen as an example). To cut the channels, I used a very narrow point carbide-tipped chisel for doing detailed work, but you can use whatever tool you typically use to create fine details. The channels don't have to be too deep (you'll spend some time filling them if they are, especially if you are not using a glue accelerator) but deep enough to ensure it does not get sanded away in the finishing process.
When adding the mica powder, I do so in layers and use CA accelerator between each layer. I squirt a little bit of CA on a working surface (a piece of cardboard will do) and mix in a small amount of the mica powder. Don't use too much powder or it will clump in the CA and become very difficult to spread. Use just enough to colour the glue. Mix it in well with the CA and, without working too slowly, start adding the colored glue to the channels (I used a small piece of dowel to do this but a wooden skewer will also work). Use an accelerator inbetween to speed up the mica layering process. If your channels are dug closely together, you can use painter's tape to cover the channels next to the one you are filling to avoid your colors accidentally mixing/spillover into an adjacent channel. Alternatively, you can sand/cut away spillover. Fill all the channels until you have the overflowing mess shown in the final image of this section.
Step 6: Trimming Down the Inlays and Final Shaping
Once the inlays have dried completely, it's time to trim them down flush with the pen barrels. I use a skew chisel but again, you can use whatever chisel works best for you. Using a high lathe speed, you can now also shape the pen into the final size you want it to be. When trimming down the blanks, make sure you do not trim down lower than the bushings (silver tubes) on the pen mandrel or the final fit of your pen and its components may be awkward. I typically trim mine down to just above the bushings.
Step 7: Oiling and Sanding
Turn down your lathe speed for the sanding process (it's easier to avoid sanding marks this way). I work through 100 - 1000 grit sandpaper and make sure that, inbetween each grit, I turn the lathe off and sand the blank all the way around using a horizontal motion covering the length of the timber. This will help to get rid of any minor sanding marks. I also wipe the blank down with a cloth after each grit to remove excess dust.
Once I have worked through all the grits, I wipe the entire pen well with a soft cloth to get rid of excess dust. I then oil the pen on the lathe using a soft cloth (a piece of old cotton T-shirt is perfect). I'm partial to linseed oil but whatever oil you prefer should work a charm. I leave this to soak in overnight.
Step 8: Adding the CA Finish
Using a bog-standard kitchen paper towel, I add about 10 layers of CA glue using a CA accelerator between coats. I start with 1-2 layers using a thick CA glue, then finish the rest using a medium CA. This is just my personal preference. You can use whatever works best for you, even thin CA. The reason I start with thick CA is that it acts like a filler for any small pores/hairline cracks left in the wood. I use a medium speed on the lathe to do this. If your lathe is too fast, you stand the chance of getting spat in the face (or eye!) with CA glue. 🤦♀️ Also, CA glue is pretty strong stuff so wear a respirator/mask during this step as they glue will heat from the friction between the paper towel and the pen blank.
Squirt a small amount (a generous drop) of glue on the paper towel and gently spread it across the length of the blank. The thick CA will dry more quickly than others so don't linger or you are liable to get paper towel stuck to your pen blank. Don't worry too much about the CA not being perfectly smooth as you're going to be wet-sanding the blank to get a shiny surface.
Step 9: Wet Sanding and Finishing the Blank
Once your CA layering is completely dry, use micro-mesh pads to wet-sand the blank (If you don't have these, use wet-sanding paper grits 1000-2000). The micro-mesh pads should be well-wet; don't use hard pressure with these against the blanks or they will end up making marks. You should simply run them along the CA-glued blank using light pressure. Run through all the pad/sandpaper grits from lowest to highest on a high lathe speed, wiping the blank inbetween coats with a soft cloth.
Once the CA layers have been wet-sanded, the final step before assembling the pen is a good polish. I use a carnauba car wax/polish, which works really well on a CA finish, but I have seen others use beeswax, jewellers rouge/polish, and other furniture/wood waxes.
Shiny! ✨
Step 10: Assembling the Pen
I don't have a pen assembly tool but you don't need one to put a pen together. I use my bench vise.
Remove the finished blanks from the pen mandrel. Check both ends of both blanks. Sometimes, a bit of CA glue can get stuck to the edges. To ensure that my pen barrel edges are smooth (for a smooth fit), I gently give them a quick sand using an 800-grit wet-sanding paper.
First, place the front end of the pen to the front end of the front-facing pen barrel. Gently seat the two pieces in the middle of your vise. Then, guiding the two ends where the front of the pen enters into the barrel with one hand, gently start closing the vise, making sure that the two pieces connect straight. Close the vise until the two pieces fit together snugly and flush.
The next part to insert is the tube connecting the two barrels (twist mechanism). This is typically (for a slimline kit) inserted up to the line indicator at the bottom of the tube. Use the same vise technique as for the tip of the pen to do this. Once I have inserted the tube up to the indicator line, I put the pen refill inside and twist it all the way out to see if the tube needs to go in a little more (based on how far the tip of the refill extends out the front of the pen).
The third part is the top-end cap and clip of the pen. Arrange these two parts together and gently stabilise them in the vise as shown in the image. Slowly begin closing the vise with one hand while holding the blank steady with the other.
Finally, put the two pen barrels together, adding the decorative ring in the middle of the pen, between the two barrels.
Step 11: Admire Your Finished Pen!
Congratulations, you've made a pen! You can now admire your handiwork and marvel at having made something that's not only aesthetically pleasing but also functional.
Shout out to the New Zealand kākāpō who inspired the coloring and shape of this pen <3
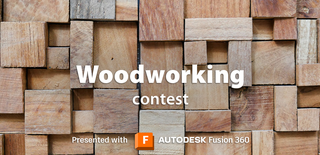
This is an entry in the
Woodworking Contest
2 Comments
3 days ago
Bird is the word.
Careful, turning can get addictive real fast haha. Respect for putting that lathe together from scratch.
4 days ago
Nice to meet another birder here - pretty much jealous about your turning skills, showing me once again the endless list of things I need to learn :D