Introduction: Custom Cutting Board With Built in Knife Holder
The idea to make this project first came to me from a picture that I saw while online of this super cool, butcher block that had a built in knife holder. I thought to myself that’s something my Grandpa would love to have, considering he is an avid hunter and he also has his own butcher shop that he runs with his friends. He also built a 1932 Ford pickup which is essentially his prized possession. So I figured, why not laser engrave that car onto the cutting board, along with my Grandpa’s name. So once I went back to the original inspiration picture I drew up my own version with the appropriate dimensions. I then started to gather the resources that I would need for this project.
Supplies
Materials list
1 common, kiln dried red oak 15In by 36 Inches
1 common, kiln dried cherry 15In by 36 Inches
Titebond 2 premium wood glue
Mineral oil
Step 1: Making Your Wood Strips
I started off with one long piece of kiln dried red oak wood that was in the rough and one piece of kiln dried cherry. I then used a radial arm saw to rough cut a number of pieces into 15in lengths.
Step 2: Measuring
After cutting the wood to rough length, I used a jointer to establish a smooth face on both the oak and the cherry wood pieces. I then jointed the edge of each piece on the jointer. Now that the material was flat and smooth, I used the 24 inch thickness planer to get the pieces to a common thickness dimension. The thicker I left the wood pieces, the fewer wood strips I would need to make the cutting board. After all of the pieces were planed to size, I moved onto the table saw to cut wood strips that would need to be 3 inches in width.
Step 3: Gluing Process
After cutting the wood strips on the table saw, I laid them out face-to-face to find out what the best design for the cutting board would be. I then glued each piece together on a gluing table face-to-face in an oak - cherry – oak - cherry pattern using a total of 17 pieces bringing the total cutting board width to 11.5” the length by 13.75” and the thickness to 3-1/8”.
Step 4: Clean Up
After the glue sat overnight, I cleaned it up using a glue scraper to get rid of the excess glue and tried to flatten the surface the best that I could.
Step 5: Shaping
Since the cutting board was glued up with the end grain on both top and bottom, I would not be able to send the glued up cutting board through the planer since it would tear up all the wood that I just glued up. To solve this issue, I designed a program in Mastercam to flatten the face of the board. After running the toolpath on one side, I flipped it over and ran the same program on the other side. This time I was able to set the final thickness of 2 inches. I then made another Mastercam toolpath design to cut the final cutting board shape.
Step 6: Making Your Knife Holder
I made another Mastercam design to cut out the knife pocket.
Step 7: Making the Juice Trench
I made one last Mastercam design to make the gravy groove to prevent any moisture from running off of the cutting board
Step 8: Making the Knife Blade Slit
After I was done with all of the Mastercam work I moved onto making the knife blade slit in the board which I did by using a miter saw set at a fixed depth and adjusting it as I lengthened the cut.
Step 9: Custom Work (optional)
I designed a laser engraving using CorelDraw X7. I designed a 32 Ford pickup graphic that I converted to vector lines and I also added my Grandfather’s name to the graphic. I then used a laser engraver to engrave my design onto the cutting board.
Step 10: Sanding and Finishing
I sanded every nook and cranny of my board until I ensured that there were no rough spots or signs of burned wood from cutting too slow on the CNC router. After my board was completely sanded I coated the entire board with mineral oil until it completely soaked in.
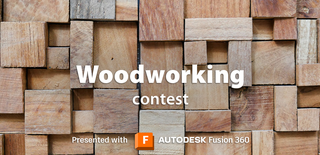
This is an entry in the
Woodworking Contest
Comments