Introduction: Engineering Mousetrap Car Design Challenge With Fusion360
The following Instructable provides a how to for running a project based learning assignment based on a distance mousetrap car contest in a College level Engineering Graphics course. Teams of 2 students each used Autodesk's fusion360 to design, simulate and manufacture a mousetrap car. Mousetrap car competitions are typically held at the highschool level, to increase the level of the challenge students were required to have complete CAD assemblies and engineering drawings of their design as well as FEA simulations of their frames performance in three point bending. The mousetrap car is an excellent design challenge because there are many aspects of the design that can be optimized. I have included a guideline to run this educational project, including the canvas files I created so you can easily implement this in your course. Many of the components of this project could be modified based on the needs of your class. For my class this project was conducted between weeks 10-17 of the semester
Supplies
Provided Construction Materials for teams:
- MDF sheet 11.8”x24”x1/8”
- 28"x8"x.008" acrylic sheets
- 12x12x0.12" acryllic sheets
- 1/4" ID ball bearings
- mouse trap
- 1/4" Wooden Dowels
- Assorted diamer 12" Wooden Dowels
- string
Tools Used:
- Ultimaker 3D printer
- Epilog Zing Laser Cutter (not needed but having a laser cutter is very useful for rapid iteration of car chassis)
- This project was conducted in the CSM makerspace and students used various tools in the tool library
Step 1: Introduce the Challange
I showed the Mark Rober YouTube video to introduce the challenge as he does an excellent job discussing the physics principles at play as well as providing a great visual way for students to understand what a mousetrap car is. For my design challenge I told the students they were not allowed to use intermediate pulleys in their design which Mark Rober shows as the world record holder design (it is actually a better design challenge if they are only allowed to directly drive from the mousetrap spring).
I then went through the rules of our contest (which can be modified for your needs) after showing the video
Design Challenge Rules:
- Vehicle must be powered by one Victor brand mouse trap measuring: 1 ¾ “ x 3 7/8 “.
- The mousetrap cannot be physically altered except for the following:
- holes can be drilled only to mount the mouse trap to a frame
- the mouse trap's snapper arm may be cut and lengthened
- Vehicles must be self-starting. They may not start with any additional potential and/or kinetic energy other than what can be stored in the mouse trap's spring.
- The spring from the mouse trap cannot be altered or heat treated.
- The mouse trap's spring cannot be wound more than its normal travel distance or 180 degrees, and you may not use any intermediate stage pullies to transfer the energy from the spring to the drive axel.
- The vehicle must steer itself and may not receive a push in any direction in order to avoid a collision.
- All vehicles will go through a compliance check to be sure that it meets all the rules.
- Each participant may have up to three trials to race their car. The best measured distance will be scored.
- The greatest linear distance will be the total distance a vehicles front wheels travel measured perpendicular from the front of the starting line to the point of the vehicle that was closest to the start line and will not "angle" to where the vehicle comes to rest.
- The Judge has the final decision as to the appropriateness of any additional materials that might be used in the construction of the vehicle. Any additional items (other than the provided materials) may not exceed a cost of 20$
- Vehicles may not be altered during the contest between trials. Repairs may be made as long as they do not include any design changes.
- At least one component of the car must be laser cut and at least 1 component must be 3D printed.
Learning Objectives:
This is a chance for you and a your group to utilize CAD to assist in the design process, and rapid manufacturing of a mousetrap car. You will use the modeling and simulation capabilities of Fusion 360 to iterate and optimize your design a mousetrap car.
A major goal of this project is to give you a chance to learn/practice the following Maker Competencies identified by UT ArlingtonLinks to an external site.:
2. Analyze the idea, question, and/or problem
- define the idea, question, and/or problem
- break the idea, question, and/or problem into its constituent parts
- question assumptions
3. Explore the idea, question, and/or problem and potential solutions
- garner input from stakeholders and peers
- research existing relevant products and ideas
- brainstorm a variety of solutions and pursue the most promising one
- evaluate the costs and benefits of using off-the-shelf parts or kits as opposed to making from scratch
6. Produce prototypes
- determine the method of creation most suited to the project
- gain confidence with technologies and processes required for creation
- specify functional requirements for prototype vs desired finished product
- divide design into individual components to facilitate testing
- document design process
7. Utilize iterative design principles
- apply measurable criteria to determine whether creation meets needs
- revise and modify prototype design over multiple iterations
- gather prototype feedback and input from stakeholders and mentors
- rework design to include insights from feedback take intelligent risks, use trial and error, and learn from failures
10. Collaborate effectively with team members and stakeholders
- listen to others
- learn from and with others
- communicate respectfully and clearly with team members and stakeholders
- follow through on team commitments and responsibilities
- practice accountability both personally and with team members
- appraise contributions to the success of the team
Design Challenge
The goal is to design a mousetrap car to travel the farthest distance. See the rules above for the complete list of the design rules.
Analysis Required
In order to optimize your design the following simulations and analysis must be completed on your model as well as design criteria met:
- Static Stress Analysis FEA Completed with the appropriate boundary conditions. To be successful the design must have a max deflection of no more than 0.5 mm , under a static load of 15 N (3.37 lbf) under 3 point bending.
Deliverables:
- A fully functional physical mousetrap car
- A fully functional Fusion360 CAD model of the final mousetrap card design
- Completed FEA analysis of your final mousetrap car design
- PDF of Working Drawings
- A website capturing your design process from start to finish (see canvas assignment for more details)
Check Points and Due Dates See checkpoint assignments on canvas.
*note for educators I have found that having many intermediate checkpoints along the way keeps students from procrastinating and has led to better quality projects.
Step 2: Introduce Finite Element Modeling in Fusion360 (optional)
I ran a guided lab where I demonstrated how students could conduct a 3 point bend test on the chassis design. See youtube tutorial video shared with students. The students were given the following basic CAD of a mousetrap design and instructed on how to do a static 3 point bend test.
Important Notes on FEA:
Engineering Graphics is a college freshman course and students were instructed on on the high level concepts and limitations of FEA but they were advised to be highly sceptical of the FEA until they had taken the proper coursework to fully appreciate the capabilities and limitations of FEA. That being said it was a great tool for students to iterate on their designs without having to build them.
Step 3: Design Checkpoint
The Goal of this assignment is to generate ideas for the project.
Come up with at least 2 different designs for the project.
A few things to consider with the designs are: (Not an exhaustive list)
- how you will manufacture the design
- how you will mount the mousetrap
- how you will secure the drive axels
What to Turn in:
Turn a brief description of each design and include answers to the following design considerations listed above. Turn in any hand drawings of the designs that help demonstrate the designs.
Be sure to include a list of what you think the advantages and disadvantages of each design are.
Only one group member will need to submit: Please include all group members names with submission
Step 4: Competition Day
Students were given 3 attempts to get the farthest distance possible. Overall this is a really fun and exciting day for the students to see how their designs performed compared to the other teams.
Step 5: Student Websites
Example Student websites:
- https://evanansgarius.wixsite.com/mouse-trap-car-team
- https://alanandsan.weebly.com/
- https://mousetrapteam7.weebly.com/
Student Prompt
You may use any free website service to create your website such as wix, weebly, google (if you use google make sure you website is accessible to anyone or you will lose points), wordpress etc.
You will be creating a website to capture the design process you went through for the project and highlight the hard work your team has done. Many employers and even some schools want to see a design portfolio of applicants, and this website can serve as a piece of your portfolio that you will be building as you continue your education. The website should reflect the pride you take in your work, and one that you would be happy to share with a potential employer as an exemplary example of the engineering work that you have done.
Deliverables: Submit a Link to your teams website (only 1 team member needs to submit)
The website should include the following sections:
- project design challenge description and need finding addressed
- design process and design evolution documented,
- Captures all intermediate designs that we studied (this is only designs that you seriously analyzed and considered, you don’t have to include things like each version saved along the way)
- Description lays out how the design was optimized
- A description of how the final design was selected and how intermediate designs were improved upon
- How prototyping was used to assist in the design process.
- Includes a Set of Working Drawings
- Project Design: A thorough description of the final design and whether you were able to meet your design objectives or not.
- Lesson Learned: A brief description of lessons learned from this project. Are there any things you wish you had done different in retrospect.
- A brief discussion of whether or not the learning objectives from this project and items from the Maker Competencies were addressed in this project. If not what do you wish would be done differently so you could be exposed to these learning objectives (see list of stated learning objectives below)
- Sources Cited: Be sure to include citations to any sources used during your project.
Step 6: Canvas Resources
I have made the assignments public so you can easily add them to your course. I added all of these in a Module in my canvas course
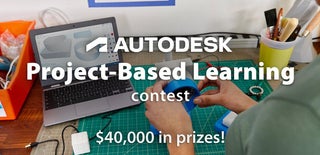
This is an entry in the
Project-Based Learning Contest
Comments
6 weeks ago
As a student myself it's very interesting to see what goes on behind the scenes of making a learning assignment. Also, I didn't know you could do structural analysis right inside Fusion 360, thank you for sharing that tip.