Introduction: Create High Quality PCB's at Home With Cheap Laser Module
Hello fellow makers!
In this Instructable I would like to take you through the process I currently use to make high quality PCB's at home using photoresist film and a cheap 405nm laser module.
When I first started making my own PCB's at home I had to use a marker to draw my design, this is a very crude method and very difficult to design anything complex.
Next I discovered transfer paper used with a laser printer, this opened up a world of opportunities as I could now design more complex boards and print them out to transfer to the boards. Unfortunately getting a the design to transfer perfectly was quite difficult and a lot of the times some of the traces pulled away from the board and I had to do a lot of touch-ups with a marker.
So I continued looking for a better way to make prototype boards...
I knew that one of the best ways to make PCB's is with a photoresist mask but process of making a mask and exposing the film always seemed like a lot of work for a quick prototype board.
Then I got thinking...
The photoresist film is exposed with UV light, what if we use readily available cheap 405nm (UV) laser engraving modules to "draw" the design directly onto sensitised PCB?
Well, IT WORKED!
And after a lot of tinkering with the settings the results are a lot better than I ever imagined, I can now make boards with 0.2mm (size of the laser dot) traces with no problems.
Step 1: What You Will Need:
To make your own you will need the following:
- 405nm Laser module
Amazon - 500mw 405nm Laser Module Kit
- 405nm Laser safety glasses ^ Included in kit ^
- CNC/3D printer/Laser engraving machine
- Photosensitive film
- PCB Design
- Copper PCB
Amazon - Single sided copper pcb
- Washing Soda
- Hydrogen Peroxide
- Hydrochloric Acid
- Water
- Disposable containers for etching process
Step 2: Design Your PCB:
There are a few options when it comes to designing PCB's but I prefer EasyEDA as it's a free to use browser based designer.
The most important part is that we want to be able to export our design to an image format as we will essentially laser engrave the image onto the photoresist.
On EasyEDA I export my design as a PNG image with it's size set to the maximum 2.5x ( see attached image ), I do this so that I can get the highest resolution picture.
Because the image is now 2.5 times larger than the original board we will need to divide size by 2.5.
On laserGRBL this is done by selecting the "autosize", then clicking on the EXIF and then deselecting the "autosize" again.
Now take the number in either the "Size W or H" and divide it by 2.5 and enter the new measurement and it will auto correct the corresponding width or height.
Step 3: OPTIONAL - Modify Your 3D Printer:
Unfortunately during this Instructable my CNC machine started to give me some problems so I had to find another way to make my PCB's.
3D Printer to the rescue!
We can use our 3d printer for the X Y movement needed to "engrave" with the laser.
First you need a way to switch the laser on and off with a PWM pulse, most instructions on the internet use the part cooling fan output but this requires either a logic converter to get the 12/24v down to the 5v required by the laser module.
Originally when I built my 3d printer I didn't like the underpowered MOSFETs used to control the heated bed/cartridge/cooler fans so I removed them and soldered pins in their place so I could connect external MOSFET boards. This made it easy for me to connect the laser to the output pin (that is already 5v) for the cooling fan.
As the laser requires very little power to expose the PCB I used the 12v power connection for the cooling tower fan as its power source.
There are many 3d printable laser mounts available on thingiverse for popular printer models, because mine is temporary I just used a piece of double sided adhesive tape to attach it to the extruder.
Step 4: Prepping the PCB:
This step is very important as any residue on the copper would cause the photoresist film to not adhere correctly and cause the traces to lift.
Start by cutting your PCB to size, this can be done by scoring it with a sharp knife and then breaking it, cutting it with a hacksaw or I always use a Dremel with an abrasive cut off wheel.
Now take some fine steel wool and give the copper a good scrub, be thorough making sure you remove all of the oxidation.
After the steel wool you should be left with a shiny copper board, now we need to take some acetone or alcohol and with a clean cloth wipe the entire board clean making sure not to touch any part with your bare hands.
Next we need to cut a piece of the photoresist film that is just slightly larger than your PCB.
- Always work with the photoresist film in a dark room or you will expose the film -
Now remove the protective plastic film from the back of the photoresist film and lay it on your PCB, we will now need to heat up the board to make the film adhere.
For this I use the heated bed of my 3d printer, simply heat it up to 80-100degrees and leave the board on it for a minute.
When the board is heated take a soft cloth and rub the film onto the board, making sure to remove any air bubbles.
We are now ready to expose the design.
Step 5: Making the Resist:
Time for the lasers!
This step will depend on which software you are using.
If you are using a Grbl based CNC/Laser engraver/Plotter then I would highly recommend LaserGRBL.
If you are using a modded 3d printer it can be more tricky but I found a great little program that takes an image and converts it to gcode that your Marlin based printer can read.
Just compose the gcode and load it onto your printer like you would if you wanted to print something.
- IMAGE TO GCODE -
With my 500mw laser I "engrave" at 1-5% power and with a speed around 1000mm/m.
You will need to experiment a bit with your power and feed rate to get the desired results as each laser module will be slightly different.
The key to getting a perfect exposure is low power with a well focused beam.
- Remember to do all of this in a dark as possible environment -
Step 6: Developing the PCB:
To remove the unexposed film we need a development solution:
Add 1 teaspoon of washing soda to about 200ml of water, you want about a 3% solution. Adjust this according to your specific brand of photoresist film. It's best to first try with a spare piece of film, you want it to take about 3 minutes to dissolve. If your mixture is too strong you'll also disolve the developed film.
Now remove the top protective film and submerge your PCB with the film into the solution.
You will see the undeveloped film starts to get opaque and dissolve into the water.
Agitate your solution until all the undeveloped film has dissolved and you are just left with the dark blue developed resist.
Rinse with clean water.
Step 7: Time to Etch:
- WEAR ALL NECESSARY SAFETY EQUIPMENT! -
In a well ventilated room or outside mix two parts hydrogen peroxide and one part of hydrochloric acid together in a separate container. Ferric Chloride can also be used instead of this solution if you have some available. (this is your etching solution so handle with care)
Tip: The hydrogen peroxide + hydrochloric acid is a safer alternative to Ferric Chloride and is great to use when making your own PCB's
Carefully submerge the PCB into the etching solution, the copper that needs to be etched has to be completely submerged and facing upwards.
Agitate the mixture regularly.
Leave it in the solution until it has dissolved all of the exposed copper leaving behind only the copper under the resist.
When done rinse thoroughly in clean water.
Step 8: Go Wild!
Now that you have your etched PCB you can drill all the necessary holes and start assembly!
This might seem like a lot of steps but after getting the hang of it you can have your PCB's ready for assembly in under 30 minutes.
And yes there are companies that can make you professional boards for pennies, the ability to make a prototype PCB at home within a few minutes is a great tool in your arsenal.
I hope you guys find this Instructable useful and if you have any questions please feel free to leave me a comment bellow.
Please share your own creations with us by clicking the "I Made It" button below.
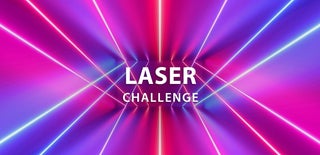
Grand Prize in the
Laser Challenge
64 Comments
1 year ago on Step 8
Very interesting instructable! I usually use the toner transfer method but it has a learning curve that I've not quite mastered yet. Your method seems simple enough and just might be the push I need to buy my first 3D printer, something I've put off for years.
Seems your method also requires a good laminator but that's also true of the toner transfer method. That method requires a really hot laminator (200 deg F) so I plan to modify an old laminator for this task. Your method maybe doesn't need one so hot?
Given the above, would you rate your method as better, worse, or about the same as the toner transfer method in terms of ease of use and quality of output?
BTW, I can't get swimming pool HCL in my area but I can get ferric chloride in granular form online. There are disposal kits available online that allow you to neutralize and solidify the spent chemical so it can be thrown away in the trash.
1 year ago
I really wish There was a way to do this without the Etching stuff and Do straight laser.
Joseph
Reply 1 year ago
I can recommend using an engraving cnc. You can get one on Amazon or Aliexpress (search for "CNC 3018") for about $150 (sometimes they are on sale for under $100). They also makes drilling holes much easier. And you don't need to use dangerous chemicals.
Reply 1 year ago
however do it on your own risk. the main danger of not burning the hydrogen and oxygen is that the hydrogen can escape the earths atmosphere due to it's extremely low weight, eventually this will result in problems when done to much. on a decent scale you can also have accumulation in specific indoor places both of oxygen and hydrogen, however this is very unlikely to happen in a home condition due to the relatively low generation of hydrogen and oxygen in a home electroplating system. still use it safely and be careful. both can be dangerous, if you do this on a quite large scale and don't safely turn it back it can turn your factory into a hydrogen bomb, or if the hydrogen escapes but the oxygen does not due to it's high weight, then any little flame or spark nearby someone or something burnable might turn everyone in that room literally to ashes, this is something that actually happens for example when the oxygen cable of a welder is damaged but this can also happen when large scale electrolysis is done unsafely. so just judge things right and only do it safely, or really small.
Reply 1 year ago
Fiber lasers can engrave metal and would be able to do this. They cost quite a bit more than a diode laser, however.
Reply 1 year ago
This is a completely different thing.
Smaller lasers may melt or burn materials, if they are very sensitive to thermal stress (like organic stuff) and if they are very bad thermal conductors (like organic matter).
Metals are good thermal conductors and the heat is dissipated before the laser spot reaches it's melting point.
Try to burn a piece of wood and a coin using a candle. You won't affect the coin in any way, no matter how long you heat up. The candle is too small.
If you want to cut/ablate metals you need to destroy atomic bonds instead of melting and for that, you need kW (pulses) of laser energy.
Reply 1 year ago
I imagine it would be really difficult to “dial in” a laser that could ablate the copper without cutting through the FR4.
1 year ago on Step 8
The process of development is still a mess and the development agent can't be used as often as the etching acid, since it oxidizes too quickly when exposed to air.
For that, I tried to use other kinds of (black) coatings, which can be removed (burned) by the laser directly, without the need of development. Just use higher laser power and rinse the pcb with water before etching. Depending on the certain type of paint used, it can be helpful to use a soft sponge when rinsing to get clear copper.
I found that acrylic paint (from a spray can) is working well and withstands the etching acid.
Since your Instructable is quite popular and read by many people, could you try this using the same PCB-design and focus length and compare the results?
My results were quite good, but I can not assess what influence my different laser focusing and higher laser power has on the result.
Reply 1 year ago
Be aware that you’re technique, is a “negative” process, whereas the one described in the instructable is a “positive” process.
(you’re removing resist/paint where you want the copper to be etched off. The photo resist “hardens” when exposed and becomes resist.)
so you’ll have to add a step of inverting black/white compared to this process.
Reply 1 year ago
I started making my own pcbs in the 1980s, but I always used pre-coated base material and didn't even notice that there are also photo-negative resists available.
May be its development agent is less gross than the photo positive variant I know, or are they chemically identical?
The problem is, that it can be used once or max. twice, since it degenerates when exposed to air quickly, while the etching acid can be used several times.
Since both can't be simply poured down the drain, I'd like to have that disposal problem as seldom as possible.
Reply 1 year ago
Yes, it’s becoming more and more difficult to be a “mad scientist” now that it’s so hard to get rid of your used chemicals…
I’m in Southern California. I can’t even get rid of stale gasoline (I keep a 5 gallon jug on hand for the generator and after a year I’d like to throw it out and buy fresh. I can’t find anywhere that they will accept it.) I can’t imagine if I called and asked if they take used ferric acid…
Reply 1 year ago
instead of paying to throw it away you can use it to light a fire, or get a scrap motor somewhere and make a generator which doesn't have to much value, then you can convert it into electricity and solve the problem. or make a steam engine run on it or just a heater to heat your house. saves money and prevents you from needing to find a place to dump it and pay a lot of money to do so.
Reply 1 year ago
Hi,
That's the first thing I tried when I got my laser, unfortunately it just did not have enough power to burn away the paint cleanly and the price for a higher power laser was just too much.
Next I used thin matt black vinyl sticker on the PCB, this worked well but the glue had to be cleaned up before etching and sometimes it would lift traces.
What I like about the resist film is that I can also "engrave" it without being stuck on something so afterwards I can transfer it to metal objects like jewelry/knives for etching.
Reply 1 year ago
Ah, Ok, I missed the "500mW" . I use a 2W laser at 50% power which works very well.
But it strongly depends on the certain paint used and I found, that it is not necessary to remove all residues completely (to get blank and shiny copper), because the remaining ashes seems to be chemically changed and can't withstand the acid.
Tip 1 year ago
One Simple Tip to make this much cheaper(for people who want it on a budged). is to use a regular 3mm or 5mm, 5v 20ma led, or a more high powered uv led. doing the calculations based on the numbers you gave you only use 5v 25ma max, this is practically the same as what those less reach. a led is not a laser, but put is in a small container(or reflector), put aluim or metal on the walls, now take a lens and put it in front of it at a certain distance depending on the lens, then you adjust the height to make the focal point of the light beam hit the film, when done right this even increases your resolution since that focal point when made properly can be as small infinity when done completely right(you work in 2d so a actual laser is not needed). in front of it until almost the distance where the PCB is should be a extra chaber this one prevents side leaking the front ins also closed but has a small hole based on what size the focussing beam should have at that point. next you can even use stepper motors and linear actuators using them(or rc servos.) you can use, or 2d print 2 straight gears and one or more round ones, then run it with a arduino and you get a super cheap version of this. it is likely more easy to move the PCB, because the lens and contraption might take up some space and weight, while you can make them very light, it is likely that moving the PCB is more easy when you use mostly scrap materials. while those less should be safe to look at, their focussed spots are not, so you can make a cardboard lid, or put it in a wooden box or such, this can also serve as framework to hold everything in place and it also keeps the film dark and you safe. this contraption should give you around half the total light power of the led on that focussed spot, so you should halve the printing speed. however you can also easily get those more powerful uv leds and use them without a reflector, and even without a lens probably, these leds are more expensive but you can get them for around €1 to €2 a piece which is a lot cheaper than the laser, and also makes it lighter and harder to damage.
if you do not have a 3d printer you can use cardboard and aluminium foil as the led enclosure, or a metal can which you can cut and fold in shape. instead of gears you can use ropes and pullys instead of a gearbox.
Question 1 year ago
"Always work with the photoresist film in a dark room or you will expose the film -
"Now remove the protective plastic film from the back of the photoresist film and lay it on your PCB, we will now need to heat up the board to make the film adhere.
"For this I use the heated bed of my 3d printer, simply heat it up to 80-100degrees and leave the board on it for a minute.
"When the board is heated take a soft cloth and rub the film onto the board, making sure to remove any air bubbles.
Wow, how do you see all that in the dark?
I was intrigued by your Instructable and went looking for the LASER MODULE you employed. Apparently, it was designed to be used with an existing 3D Printer - Plug n Ply?
In the product description on Amazon, they included scarps of plywood to test burning images into/onto the wood. I am learning more about this multi-dimensional s**t! Thanks
Answer 1 year ago
Get yourself a cheap 1 Watt red or yellow LED lamp! In industrial settings where they use this kind of film, they use yellow lights (see here https://youtu.be/ljOoGyCso8s?t=265 for example) since that's the wavelength where the film is the least sensitive, but we still can see. Same principle for red, but we can't se that well. It's useful if your film is sensitive to more colors of light other than just the 405nm of the photoresist, for example when developing photographic film (remember the red-lit darkrooms?)
Answer 1 year ago
Haha! I'm South African...we see in the dark :D
There are some kits available that are plug and play like the ones for the Ender 3/5's but for the generic modules like mine you are going to need to find an available pin on your motherboard to give a TTL signal to the module, this is usually done by using the signal to the part cooling fan.
1 year ago
I bet you could also use the lazer module for the solder mask as well! https://www.amazon.com/dp/B01MUB4PJL
Reply 1 year ago
They're sensitive to the same 405nm, it should work!