Introduction: Floating Pieces Purse
In this instructable I'll show you how to make a purse made of floating pieces. My favorite version is made of wood, but I also shared some files for a 3D printed version.
The idea for the purse came from various inspirations here on the site. First, I wanted to make something out of wood for the Wear It contest, so I decided to make a purse. Inspired by Penelopy Bulnick's insutrctables about 3D printing onto fabric (here!), I thought I'm going to make a flexible bag. But after several prototypes and lots of weekend hours, I got to my final design you'll see here. The design is made mostly of wood and has a flexible cover and magnetic snaps. I really like how it turned out, and it is surprsingly lightweight. I hope you enjoy this projects as much as I did!
For those who might prefer a narrated version of the project, here's a short video about it:
If you have any questions or comments, feel free to leave them in the comment section at the bottom!
Supplies
Materials:
- 3mm plywood of your favorite type (about 500mm x 400mm in total)
- Dark fabric for lining (optional)
- All-purpose gel glue, or some wood glue
- A strap or more dark fabric to make one
- Dark water-based color (optional)
- Magnets (these should work <- affiliate link!). I used 30x10x2 magnets (that's their width, heigth and thickness in mm)
Tools:
- Laser cutter (or access to one!)
- OR a 3D printer
- A ruler, a pencil and a few other things you definitely have :)
Step 1: Design
The purse is made of 5 outer faces and an inner skeleton. I designed the pieces a 2-dimensional drawing. The outer shell is made of many individual parts with 1mm (about 1/25") spacing between them. To hold the pieces together I ended up making a thin skeleton that is attached to all of the floating pieces, holding everything in place. To export the files as DXF, I used the Export as DXF option in TINKERCAD. I also wanted the bag to have a flexible cover, so I added a living hinge to the top using LightBurn (taken from an old project of mine roll top pencil case).
The file below includes the parts that make up the skeleton as well as the outer shell. The corresponding parts are laid next to each other in that SVG file. Make sure you keep track of which skeleton part belongs to which outer face!
Floating Pieces Purse
Step 2: Prototypes
I went through a lot until I reached the final design. I had a vision for how the bag is going to look like - it's going to be made of many pieces as if it's broken, but somehow held in place. So I started prototyping. As most people visit instructables for inspiration, I figured the prototyping step is worth sharing - I really liked some of the concepts, but they didn't fit this specific project.
At first, I thought the bag should be flexible. So, inspired by Penelopy Bulnick's insutrctables about 3D printing onto fabric, I decided to glue the pieces of wood onto a piece of fabric. This turned out pretty cool - you can flex the sheet a lot towards the fabric side, but not towards the wood side. You can decide how much flex to want to have towards the wood side by adjusting the spacing between adjacent pieces (see 3rd image), and it's even easy to calculate the maximum flexing angle at each intersection using simple geometry. I tried and tested many different spacings. The key here is to vary the spacing with respect the width of the wood you'll be using. So if you use 3mm wood like I used, 3mm spacing would allow for 90 degree bends.
I cut the pieces of wood on my laser cutter, put glue over each piece while it's still on the honeycomb, and laid the fabric over it. This way, the little piece of wood were kind of like a puzzle already assembled in place. Once the glue dried I just pulled it off, which resulted in perfectly ordered pieces of puzzle attached to the cloth you see in the 4th image.
I then glue the different faces of the bag together. The result were far from perfect, and I really didn't like the flexibility of the bag after all.
Next, I made a rigid bag with a solid inner skeleton to hold the pieces of wood together. This one turned out way too bulky to be an actual accessory (I think?).
So I ended up making a smaller bag, with a flexible round top, which is what you'll see in the next steps.
Step 3: Cut Frames
Let's get to business!
- Cut the skeleton pieces. It's essential to cut these parts first because you want them clean and ready for step 5.
- Remove the pieces that were left in between the frames.
- Keep track of who's skeleton piece belongs to which face, as they're all different!
Tip - notice that I painted one side of the frames with a dark brown color. This will make the inner skeleton less visible from the outside.
Step 4: Cut Outer Shell
Now cut the outer shell. Once the parts are cut, leave them inside your laser cutter for a little longer. They should look like a solved puzzle (see second image), and we'll use that in the next steps.
Step 5: Glue Frame to the Floating Pieces
Apply plenty of glue to the painted side of one of the skeleton pieces. I used transparent all-purpose gel glue (Scotch), and it worked great. Next, lay it over the corresponding outer shell that's waiting in your laser cutter. The skeleton holds all the floating pieces in place, so make sure it's aligned properly. Repeat this for all 5 outer faces. For the front and back faces, leave a 6mm spacing on each side, marked with a pencil. This is essential so that the right and left faces can fit later on.
Once the skeletons are attached to their corresponding outer faces, remove everything from your laser cutter. If any of the spacers get stuck, use tweezers or a utility knife to push them out, and if any of the floating pieces accidently move, just shift them back to place before the glue is completely dry.
Step 6: Assemble the Bag
You should now have all 5 pieces, each made of floating pieces attached to a thin inner skeleton.
- Lay the pieces on a flat surface (first image).
- Attach the outer faces to the bottom one by one. The backside with the living hinge should be attached last.
- As you go, make sure the edges are flush, and that you clean up any excess glue before it dries.
Double check that everything looks fine, and let the glue dry.
Step 7: Curve the Living Hinge
Since the purse will be closed most of the time, it's wise to ease some tension off the living hinge.
- Remove some material off the edge of the front face by sanding (see first & second images).
Next:
- Close the purse with rubber bands
- Spray some water over it
- Let the purse dry completely for an hour or two.
This process will reduce stress off the living hinge by adding a permanent bend to it.
Step 8: Sand
To reach a more polished look, sand all the edges until they're round and smooth. Also, spraying the flexible top with water (step 7) will increase the grain of your wood, so you should sand the top as well. Just sand everything :)
Step 9: Add Magnets
To add magnets, mark the center of the front of the living hinge (the flexible top), and glue a strong magnet to it (first image).
Once the magnet on the outside is glued firmly, attach magnets to the front face of the purse such that it aligns with the previous one (second image). I used gray epoxy glue for this, which was a huge mistake since it made a ton of mess. You should use something transparent for this step.
Step 10: Add a Strap
Add a strap. I decided to keep it simple and use a thin piece of brown fabric. Cut the fabric into the desired width (1cm / 0.5" worked nicely for me), and thread it through the holes in the side faces. To secure the strap, you can tie a inside the bag. I used a couple of key chains so that the length of the strap is adjustable (see third image).
Another great choice would be to make a strap out of leather or buy one that fits the bag.
Step 11: Optional - 3D Printed Version
The design I came up with for the 3D printed version is not 100% optimized for printing. You could make it lighter, rounder, and include joints in the design. But I didn't! So this design is very similar to the wooden one. The major changes are that most of it is printed assembled, and some changes were made to the living hinge.
The main drawbacks of the design are that the living hinge is a bit too stiff, and that it doesn't have a proper solution for the closure.
If you do decide to print it, you'll need to print 5 individual pieces (bottom, front, back+flexible top, right & left). They're all attached here. Then, you'll need to add a bag closure. I used a rubber band and a button from a pair of old jeans (see second image). Moreover, to relief the tension off the living hinge, I had to use a hair dryer while holding it in its closed position. This worked pretty well, but you should be careful not to melt it entirely.
Overall, it makes for a pretty nice box, but I'd say that the 3D printed version is a bit too bulky to make for a shoulder bag or a purse. You decide :)
Attachments
Step 12: Enjoy!
That's all for today! I hope you enjoyed reading and that some of this article inspired you to make something of your own!
If you like my instructable and want to see more, you're welcome
to visit my instructables page, my website, or the collection of my laser-cut projects
And if you want to support my work (for free), visit my YouTube channel, see if you like what I've done so far, and consider subscribing! See you soon :)
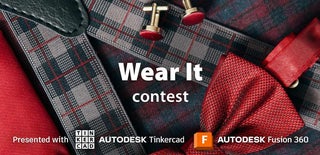
First Prize in the
Wear It Contest
8 Comments
19 days ago
Congratulations, Nir!! Well deserved. Really beautiful work.
Reply 18 days ago
Thank you Brana! I was really surprised with what the judges thought of this
:) I enjoyed this project so much, but I thought people would think it's too odd!
19 days ago
Congratulations for win First Prize !
Reply 18 days ago
Thanks!! :)
6 weeks ago
Wow, really nice work. And the pictures are great :-).
Reply 6 weeks ago
thanks!!
6 weeks ago
Ohhh I love the look of this bag! Really nicely done :D
Reply 6 weeks ago
Thanks jessy! I'm especially happy with this project, I'm glad you like it:)