Introduction: Gas Forge
Hey everyone, today I have an amazing project for you to make. What are the best builds? - The ones that open the door to a whole new world of future projects. This gas forge enables you to get to know the awesomeness of blacksmithing. So follow along and build your own!
Supplies
I want to start of by saying that these are not instructions that have to be followed to the T. Lots of my choices were due to the circumstances I was given and other options would be totally fine as well. This is also why I won't provide exact measurements for the build but more of a recipe that can be applied to every possible gas canister and burner configuration.
I also want to clarify that although I did my best I am by no means an expert on this topic and there are people who went way way more in depth on all of these points. If you have any questions you can of course ask me here or you can go to this forum where every last detail to the science of forge building has been laid out and discussed thoroughly. Many components of my forge are inspired by this site.
As of materials you will need:
- an empty gas canister(I used an 11kg Propane bottle)
- some 6mm steel plate
- some 2mm steel plate
- some 20mm*4mm steel bar
- some 20mm steel round bar
- some sealant for your pipe connections (I used Loctite but a designated gas sealant would be preferable)
- enough ceramic fiber blanket for two layers on the inside of your forge
- fire resistant cement
- fumed silica powder or some other form of rigidizer for the ceramic blanket
- heat resistant spray paint (mine is rated for up to 800C)
- 1x steel pipe 100mm*1 1/2''
- 8x M6 machine screws to secure the burners to the forge
- 2x M6 machine screw with nuts and washers to form the hinges of the air regulator caps
- 1x pressure regulator
- 1x hose breakage protection 3/8"
- 1x 3m gas hose 3/8"
- 1x pipe connector 3/8" left hand thread --> 3/8" right hand thread
- 1x bell reducer 3/8" --> 1/4" stainless steel
- 1x male/ female ball valve 1/4"
- 1x reduction connector male/ male 1/4" --> 1/8"
- 1x 90deg elbow 1/8" stainless steel
- 1x tee 1/8" stainless steel
- 3x pipe nipple 100mm*1/8"
- 2x mig welding tips 0.6mm
- 2x bell reducer 1 1/2" --> 3/4"
- 2x pipe nipple 150mm*3/4"
- 2x bell reducer 1" --> 3/4" stainless steel
In case you couldn't find non galvanized pipe nipples and bell reducers you will need some sort of acid to de-galvanize them.
As of tools you will need the basic hand tools of a small workshop. In addition there are some "special" tools you will need:
- a welding machine
- a thread cutting set + lubrication
- a drill (a drill press would be even better)
- an angle grinder
- a metal hole saw (32mm in diameter for me)
Step 1: Prepping the Tubing
In case some of your pipes are galvanized, you need to let them sit in some acid to get rid of the galvanization, since welding or heating the zinc coating to high temperatures can cause toxic fumes to be released. I used hydrochloric acid but something less aggressive like concentrated vinegar works too it just takes longer. When handling acids always wear latex gloves and eye protection and in this case also a respirator. Depending on how strong your acid is and on how much water you add this step can take anywhere from minutes to days. Once the zinc coating has come of you need to neutralize the remaining acid that's on the metal otherwise it will keep eating away. Use bleach or baking soda and borax for this step. When you're done just rinse the pieces off with some water.
Step 2: The Burners (Part 1)
Before starting trace the outline of the 1 1/2" bell reducer onto a piece 2mm steel plate, you will need this in the next step.
Now start by flattening the 1 1/2" opening of the bell reducers to make the best possible seal. Then drill a straight hole through the bell reducer that fits the 1/8" pipe nipple.
Connect the two 1/8" pipe nipples to the tee using a sealant to make the connection gas tight. Drill two holes into the underside of these pipe nipples. The spacing of these holes determines the spacing of your two burners. Thread the holes to fit a standard 0.6mm mig welding tip.
Feed the pipe nipples through the holes in the bell reducers and screw in the mig tips through the smaller opening. Make sure to use sealant. A pair of long thin pliers are helpful here.
Straighten everything out and then weld the pipenipple to the bell reducers making sure to make the welds air tight. Then weld shut the openings of the pipe nipples sticking out of the bell reducers.
Step 3: The Burners (part 2)
Start by cutting out the circle shapes draw in the last step and make sure to leave an extra bit sticking out for the hinge. Weld a piece of scrap metal to each bell reducer as a counterpart to the hinge. Then drill a hole through both the hinge on the cap and the hinge on the bell reducer. Weld a piece of scrap metal to each cap to have something more comfortable to grab when opening and shutting the air flow. Use screws to attach the sliding caps to the bell reducers.
Assemble the rest of the burners as shown in the pictures. Again make sure to use sealant.
It is helpful to check for any unwanted gas leaks by submerging the whole burner assembly under water and turning the gas on.
Now you can mount the burners to a sturdy surface and test them. Play with gas pressure at the pressure regulator and air flow with the sliding caps on the bell reducers to find the balance for a nice blue flame.
NEVER start the burners in an enclosed space or otherwise poorly ventilated area.
Step 4: The Forge Body
DO NOT cut into the bottle immediately even if it is empty!!! There could be rest gas in the bottle that could ignite from the sparks of an angle grinder.
After completely emptying the bottle unscrew the valve using a big pair of pliers or a wrench in combination with a hammer. This requires a lot of force and patience since the valve sits super tight. Once you unscrewed it fill the whole bottle with water to make sure there is absolutely no gas left inside. Pour out the water.
Now you are ready to cut of the handels and stand. Proceed with marking the line along which you will cut open the bottle in the next step and the openings on the front and back side of the forge. You can use rigs similar to the ones I used in the pictures to get accurate markings.
Cut out the front and the back opening you just marked.
Step 5: Prepping the Openings
Grab a piece of 6mm steel plate and mark the curvature of the forge body by holding it to the surface that it is going to connect to. Now cut out the curvature using the technique shown in the picture. Repeat this for both openings. Don't weld the plates on yet.
Now cut off the top of the can along the line you marked earlier.
From 4mm*20mm steel bar cut three pieces to make a frame for the larger opening. Use the same technique as used earlier to get the curvature of the can onto the steel bar. You can use magnets to get a good idea of how the pieces are going to join up. Build a rig to weld the frame pieces together. Don't weld this on yet either.
If you want to you can also build a frame for the smaller back opening. For me it was not worth the effort. But it would provide a better seal to improve fuel efficiency.
Step 6: Insulating the Forge
!!! Before unpacking the ceramic fiber blanket put on a respirator and latex gloves, since inhaling the dust of these blankets is extremely toxic and dangerous.
Cut the blanket in a way that you end up with two layers of insulation lining the forge as can be seen in the pictures (the ends only need one layer). After placing the lid back onto the body use a knife or a hacksaw blade to cut out the openings. Then weld on the cap making sure the bottoms of both openings line up perfectly eventually forming a flat surface on the inside of the forge.
Now the ceramic blanket needs to be rigidized, so that it isn't a breathing hazard anymore. For this, first wet the inside of the forge thoroughly using a spray bottle. Now mix some fumed silica with water and add some food coloring to make the solution visible so you can ensure an even coverage. Then spray the solution onto the ceramic wool. Cover every single inch, there is no "using too much". This coating will protect your lungs from the tiny ceramic needles that now can't be released into the air anymore. Let the whole thing dry out for a couple of days to make the rigidizer set properly. You can fire up the forge for a couple of minutes to speed up this process.
(As you might have noticed the pictures here don't line up with the progress of the build. This is because I added the rigidizer at a later point. I should have done it at this point instead - just as soon as possible.)
Now is also a good time to remove the paint from the canister. Use either paint stripper or a sanding disc on the angle grinder.
Step 7: Welding the Openings
Now it is time to attach the steel plates and the frames around the front opening.
to ensure that the front and back plate are perfectly parallel and level, use a rig as shown in the pictures.
Step 8: Adding Feet and Burner Mounts
Cut four pieces of 20mm steel round bar to form four stands for your forge. Mark their place on the forge base and weld them in place.
Now drill holes into the forge roof slightly offset to the side. Use a drill that matches the inner diameter of the10mm* 1 1/2" steel pipe. Use a thin blade or a sharpened hacksaw blade to cut out the holes from the ceramic blanket.
For the burner mount mark a point on all four sides of the 1 1/2" pie and drill holes. Now thread the holes and cut the pipe into the two parts as shown in the pictures. Weld the mounts onto to holes.
Step 9: Pouring the Concrete Floor
Now it is time to pour the concrete floor in order to protect the ceramic blanket underneath.
First wet the surface you are pouring onto using some water and a spray bottle, this helps the concrete to stick properly.
Mix the concrete according to the instructions provided by the packaging or the seller. If needed use a cut up bottle to get the concrete into the forge.
The concrete needs a high moisture environment to set properly so when you're done pouring place the whole forge into a plastic bag adding a tub of water and then sealing the bag as shown in the picture. Leave the forge in the bag for at least 24 hours, preferably 48 hours and then let the forge air dry until it is ready to paint.
Step 10: Coating the Metal Black
Finally to protect the forge from rust, apply a coating of heat resistant spray paint to all metal parts. If necessary tape of parts you don't want to be painted. Let the paint sit for 24 hours or however long is recommended by the manufacturer.
Now your forge is ready to use! Stick the burners into the openings and secure them in place with four screws each.
Light the forge using a gas torch or a burning piece of paper, placed in the forge before turning on the gas.
Congrats! You're done and you can start making literally anything, your creativity is your only limit, and even for that there is instructables or Pinterest ;)
Thanks for reading along, enjoy!
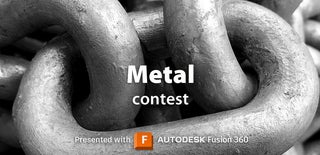
Second Prize in the
Metal Contest
Comments